Filter presses are widely used in various industries for solid-liquid separation processes. They offer efficient filtration and dewatering solutions, making them a valuable asset for many businesses. In this blog post, we will delve into the world of filter presses, exploring their applications, working principle, benefits, and key considerations for selecting the right filter press for your specific needs.
- Understanding the Working Principle of a Filter Press: A filter press consists of a series of chambers containing filter plates and filter cloths. The process begins by pumping a slurry or a suspension into the filter press, which then undergoes filtration. The solid particles are retained by the filter cloths, while the filtrate passes through the filter plates and collects in a designated outlet. The filtration process continues until the chambers are filled with solids.
- Applications of Filter Presses in Various Industries: a. Chemical Industry: Filter presses are commonly used in the chemical industry for separating and clarifying liquid solutions, recovering valuable chemicals, and removing impurities or contaminants from process streams.
b. Mining and Metallurgy: Filter presses play a crucial role in mining and metallurgical processes. They are utilized for dewatering mining slurries, concentrating metal ores, and reducing the moisture content of tailings or concentrates.
c. Pharmaceutical Industry: In the pharmaceutical industry, filter presses are employed for separating solids from liquids in the production of active pharmaceutical ingredients (APIs), recovering crystals, and purifying drug compounds.
d. Food and Beverage Industry: Filter presses find applications in the food and beverage sector for clarifying juices, filtering wine, processing edible oils, and removing impurities from liquid food products.
e. Municipal and Industrial Wastewater Treatment: Filter presses are extensively used in wastewater treatment plants to dewater sludge and reduce its volume, resulting in more efficient disposal and potential recovery of valuable resources.
- Benefits of Using a Filter Press: a. Efficient Solid-Liquid Separation: Filter presses offer high efficiency in separating solids from liquids, resulting in a dry cake and a clarified filtrate.
b. High Filtration Rates: The design of filter presses allows for rapid filtration, enabling businesses to process large volumes of slurry or suspension in a relatively short period.
c. Versatility: Filter presses can accommodate a wide range of filtration applications, thanks to the availability of various filter cloths and plates with different pore sizes and materials.
d. Cost-effective Solution: Filter presses provide a cost-effective filtration solution by minimizing the volume of waste generated, reducing disposal costs, and potentially recovering valuable materials.
- Key Considerations for Selecting a Filter Press: a. Filtration Requirements: Consider the particle size, type of solids, and desired filtration rate to choose the appropriate filter press design and filter media.
b. Size and Capacity: Assess the required filtration capacity and available space to determine the optimal size and configuration of the filter press.
c. Maintenance and Operation: Evaluate the ease of operation, maintenance requirements, and availability of spare parts and technical support.
d. Ancillary Equipment: Consider the need for additional equipment, such as pumps, sludge feed systems, and cake discharge mechanisms, to ensure seamless integration with the filter press.
Conclusion: Filter presses are indispensable tools in numerous industries, providing efficient and reliable solid-liquid separation solutions. By understanding their working principle, exploring their applications, and considering key selection factors, businesses can make informed decisions when choosing a filter press that best meets their filtration requirements. Implementing a filter press can lead to improved productivity, cost savings, and enhanced environmental sustainability in various industrial processes.
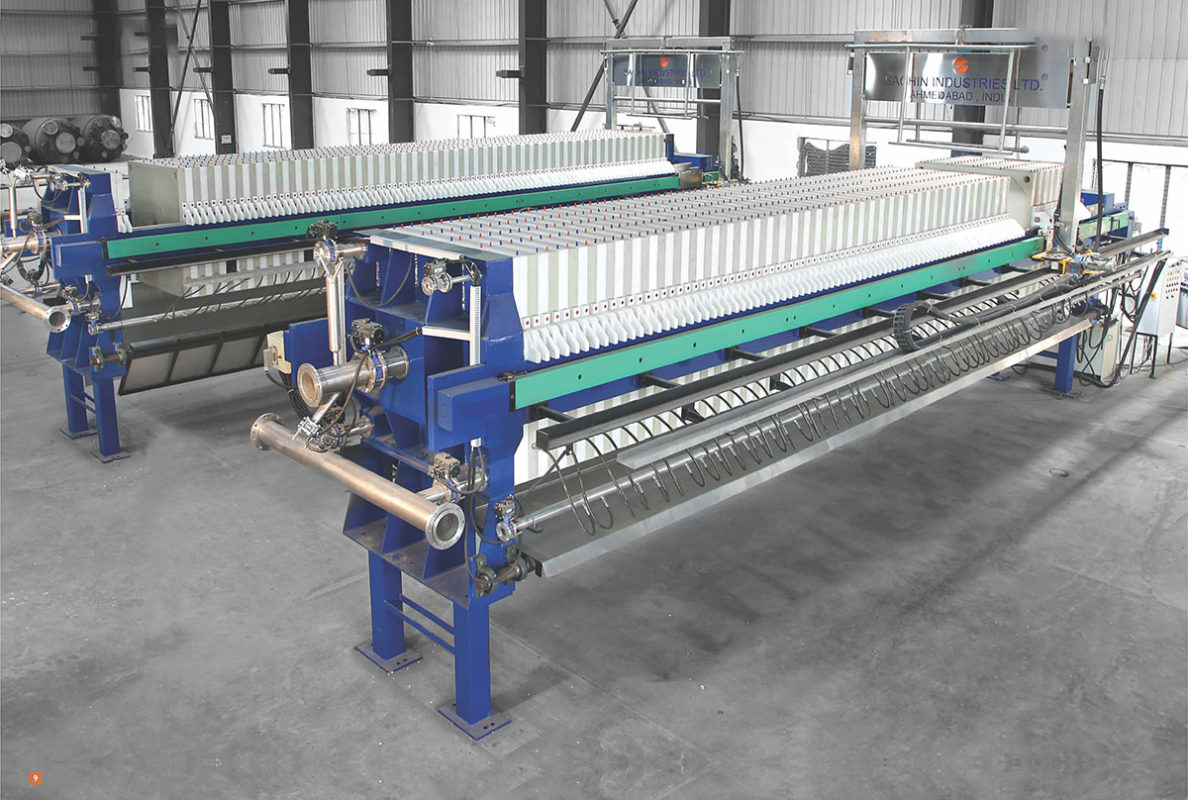